How to design a feasible plastic part
You have a very good idea for a new product, but after completing the drawing, your supplier tells you that this part can not be injection molded. Let’s see what we should notice when designing a new plastic part.
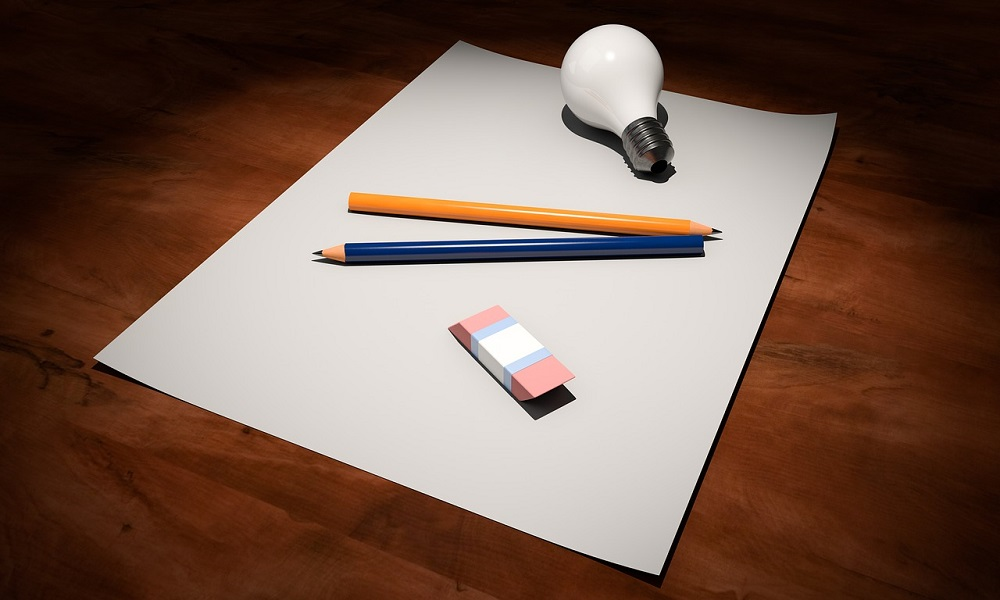
Wall thickness –
Maybe all plastic injection molding engineers would suggest to make the wall thickness as uniform as possible. It is easy to understand, the thicker sector shrink more than the thinner sector, which cause warpage or sink mark.
Take the consideration of part strength and economic, in case of enough stiffness, wall thickness should be as thin as possible. Thinner wall thickness could make the injection molded part cool faster, save the part weight and make the product more efficient.
If the unique wall thickness is a must, then make the thickness vary smoothly, and try to optimize the mold structure to avoid problem of sink mark and warpage.
Corners –
It is obvious that corner thickness will be more than normal thickness. So it is generally suggested to smoothen the sharp corner by using radius on both the external corner and internal corner. The molten plastic flow will have less resistance when going thought the curved corner.
Ribs –
Ribs can strength the plastic part, another usage is to avoid the twisted problem on the long, thin plastic housing.
Thickness should not be as the same as wall thickness, about 0.5 times of wall thickness is recommended.
Rib base should have radius and 0.5 degree draft angle.
Don’t lay ribs too close, keep a distance of about 2.5 times of wall thickness between them.
Undercut –
Reduce the number of undercuts, it will increase the complication of mould design and also enlarge the failure risk.
Post time: Aug-23-2021