Injection molding is a manufacturing process widely used in the production of small appliances. The process involves injecting molten material into a mold cavity where the material solidifies to form the desired product. However, like any manufacturing process, injection molding has its challenges. Common defects can occur during the injection molding process, affecting the quality and functionality of the final product.
1. Short shots
A common defect in injection molding of small appliances is “short shots.” This occurs when the molten material does not completely fill the mold cavity, resulting in an incomplete or undersized part. Short shots can be caused by a variety of factors, such as insufficient injection pressure, improper mold design, or insufficient material temperature. To prevent short shots, injection parameters must be optimized and proper mold design and material temperature ensured.
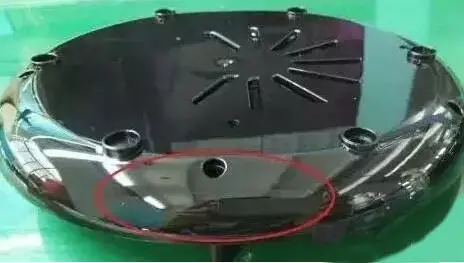
2. Sink marks
Another common defect is “sink marks,” which are depressions or dents in the surface of the molded part. When a material cools and shrinks unevenly, sink marks may occur, causing localized depressions in the surface. This defect is usually caused by insufficient holding pressure, insufficient cooling time, or improper gate design. To minimize sink marks, it is critical to optimize the packing and cooling phases of the injection molding process and consider gate design modifications.
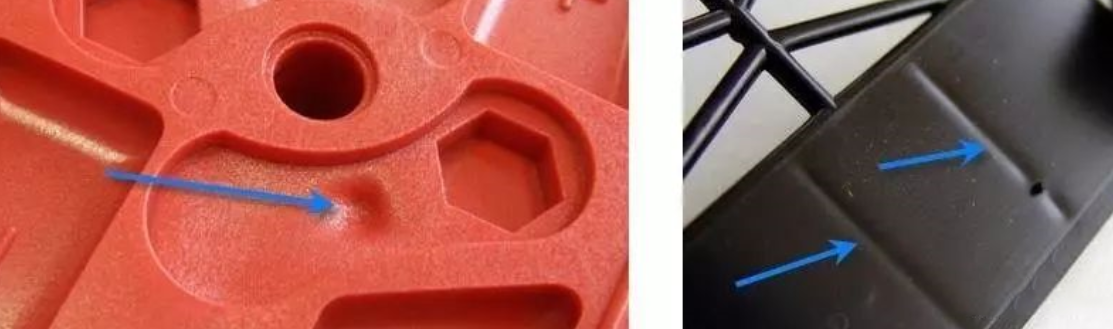
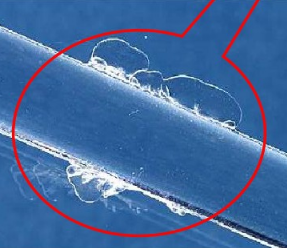
3. Flash
“Flash” is another common defect in injection molding characterized by excess material extending from the parting line or edge of the mold. Burrs may occur due to excessive injection pressure, worn mold parts, or insufficient clamping force. To prevent flashing, it is important to regularly maintain and inspect molds, optimize clamping force, and carefully monitor injection pressure.
In conclusion, while injection molding is an efficient manufacturing process for small home appliances, it is important to be aware of the common defects that can occur. By understanding and solving problems such as short shots, sink marks and flash, manufacturers can improve the quality and consistency of their injection molded products. Through careful process optimization and mold maintenance, these common defects can be minimized, ensuring high-quality small appliances produced through injection molding.
Post time: Mar-26-2024