ත්රිමාණ මුද්රණය ඉන්ජෙක්ෂන් මෝල්ඩින්ට වඩා හොඳද යන්න තීරණය කිරීම සඳහා, ඒවා සාධක කිහිපයකට එරෙහිව සංසන්දනය කිරීම වටී: පිරිවැය, නිෂ්පාදන පරිමාව, ද්රව්ය විකල්ප, වේගය සහ සංකීර්ණත්වය. සෑම තාක්ෂණයකටම එහි දුර්වලතා සහ ශක්තීන් ඇත; එබැවින්, කුමන එකක් භාවිතා කළ යුතුද යන්න ව්යාපෘතියේ අවශ්යතා මත පමණක් රඳා පවතී.
දී ඇති අවස්ථාවකට වඩා හොඳ කුමක්ද යන්න තීරණය කිරීම සඳහා ත්රිමාණ මුද්රණය සහ ඉන්ජෙක්ෂන් මෝල්ඩින් සංසන්දනයක් මෙන්න:
1. නිෂ්පාදන පරිමාව
එන්නත් අච්චු ගැසීම: ඉහළ පරිමාවක් භාවිතා කිරීම
ඉන්ජෙක්ෂන් මෝල්ඩින් මහා පරිමාණ නිෂ්පාදනය සඳහා ඉතා සුදුසු ය. අච්චුව සෑදූ පසු, එය අතිශය වේගවත් වේගයකින් එකම කොටස් මිලියන දහස් ගණනක් නිපදවනු ඇත. ඉතා වේගවත් වේගයකින් ඒකකයකට ඉතා අඩු වියදමකින් කොටස් නිෂ්පාදනය කළ හැකි බැවින් එය විශාල ධාවනය සඳහා ඉතා කාර්යක්ෂම වේ.
සුදුසු වන්නේ: මහා පරිමාණ නිෂ්පාදනය, ස්ථාවර ගුණාත්මකභාවය අත්යවශ්ය කොටස් සහ විශාල ප්රමාණ සඳහා පරිමාණයේ ආර්ථිකය.
ත්රිමාණ මුද්රණය: අඩු සිට මධ්යම පරිමාණය දක්වා හොඳම
ත්රිමාණ මුද්රණය අඩු සිට මධ්යම ප්රමාණය දක්වා ධාවනයක් අවශ්ය නිෂ්පාදන සඳහා සුදුසු වේ. අච්චුවක් අවශ්ය නොවන බැවින් ත්රිමාණ මුද්රණ යන්ත්රයක් සැකසීම සඳහා අච්චු පිරිවැය අඩු වුවද, බර පරිමාවන් සඳහා එක් එක් කැබැල්ල සඳහා පිරිවැය සාධාරණ ලෙස වැඩි වේ. නැවතත්, මහා පරිමාණ නිෂ්පාදන හොඳින් ගැලපෙන්නේ නැත, එන්නත් අච්චු නිෂ්පාදනයකට සාපේක්ෂව මන්දගාමී වන අතර විශාල කාණ්ඩ මගින් ඉතිරි කළ නොහැක.
සුදුසු වන්නේ: මූලාකෘතිකරණය, කුඩා නිෂ්පාදන ධාවනය, අභිරුචි හෝ ඉතා විශේෂිත කොටස්.
2. පිරිවැය
ඉන්ජෙක්ෂන් මෝල්ඩින්: ඉහළ ආරම්භක ආයෝජනය, අඩු ඒකකයක පිරිවැය
අභිරුචි අච්චු, මෙවලම් සහ යන්ත්ර සෑදීම මිල අධික බැවින්, මූලික සැකසුම සැකසීම මිල අධික වේ; කෙසේ වෙතත්, අච්චු නිර්මාණය කළ පසු, නිෂ්පාදනය වැඩි වන තරමට කොටසක පිරිවැය විශාල ලෙස අඩු වේ.
හොඳම දේ: එක් එක් කොටසෙහි පිරිවැය අඩු කිරීමෙන් මූලික ආයෝජනය කාලයත් සමඟ ආපසු ලබා ගන්නා ඉහළ පරිමාණ නිෂ්පාදන ව්යාපෘති.
ත්රිමාණ මුද්රණය: අඩු මූලික ආයෝජනය, ඒකකයකට වැඩි පිරිවැය
අච්චු හෝ විශේෂිත මෙවලම් අවශ්ය නොවන බැවින් ත්රිමාණ මුද්රණයේ මූලික පිරිවැය සාපේක්ෂව අඩුය. කෙසේ වෙතත්, ඒකකයකට පිරිවැය එන්නත් අච්චු ගැසීමට වඩා වැඩි විය හැකිය, විශේෂයෙන් විශාල කොටස් හෝ ඉහළ පරිමාවන් සඳහා. ද්රව්ය පිරිවැය, මුද්රණ කාලය සහ පසු සැකසුම් ඉක්මනින් එකතු විය හැකිය.
සුදුසුම දේ: මූලාකෘතිකරණය, අඩු පරිමාවකින් යුත් නිෂ්පාදනය, අභිරුචි හෝ තනි කොටස්.
3.නිර්මාණයේ නම්යශීලී බව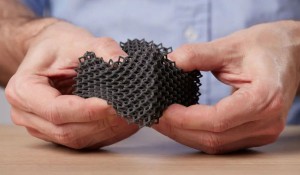
එන්නත් අච්චු කිරීම: එතරම් බහුකාර්ය නොවේ, නමුත් ඉතා නිවැරදියි.
අච්චුව සෑදූ පසු, මෝස්තරයක් වෙනස් කිරීම මිල අධික හා කාලය ගතවන ක්රියාවකි. නිර්මාණකරුවන් අච්චුවේ යටි කැපුම් සහ කෙටුම්පත් කෝණ අනුව සීමාවන් සලකා බැලිය යුතුය. කෙසේ වෙතත්, ඉන්ජෙක්ෂන් මෝල්ඩින් මඟින් නිරවද්ය ඉවසීම් සහ සුමට නිමාවක් ඇති කොටස් නිපදවිය හැකිය.
සුදුසු වන්නේ: ස්ථාවර මෝස්තර සහ ඉහළ නිරවද්යතාවයක් සහිත කොටස්.
ත්රිමාණ මුද්රණය: ප්රමාණවත් තරම් නම්යශීලී සහ අවශ්ය අච්චු සීමාවකින් තොරව
ත්රිමාණ මුද්රණය සමඟ, ඔබට ඉන්ජෙක්ෂන් මෝල්ඩින් සමඟ කළ නොහැකි හෝ ආර්ථික වශයෙන් කළ නොහැකි ඉතා සංකීර්ණ සහ සවිස්තරාත්මක නිර්මාණ නිර්මාණය කළ හැකිය. යටි කැපුම් හෝ කෙටුම්පත් කෝණ වැනි සැලසුමට සීමාවක් නොමැති අතර, නව මෙවලම් නොමැතිව ඔබට ඉතා කෙටි කාලයක් තුළ වෙනස්කම් කළ හැකිය.
හොඳම දේ: සංකීර්ණ ජ්යාමිතීන්, මූලාකෘති සහ බොහෝ විට නිර්මාණයේ වෙනස්කම් වලට භාජනය වන කොටස්.
4.ද්රව්ය විකල්ප
ඉන්ජෙක්ෂන් මෝල්ඩින්: ඉතා බහුකාර්ය ද්රව්ය විකල්ප
ඉන්ජෙක්ෂන් මෝල්ඩින් පුළුල් පරාසයක පොලිමර්, ඉලාස්ටෝමර්, පොලිමර් සංයුක්ත සහ අධි ශක්ති තාප කට්ටල සඳහා සහය දක්වයි. මෙම ක්රියාවලිය වඩා හොඳ යාන්ත්රික ගුණ සහිත ශක්තිමත් ක්රියාකාරී කොටස් නිෂ්පාදනය සඳහා යොදා ගනී.
සුදුසු වන්නේ: විවිධ ප්ලාස්ටික් සහ සංයුක්ත ද්රව්යවල ක්රියාකාරී, කල් පවතින කොටස්.
ත්රිමාණ මුද්රණය: සීමිත ද්රව්ය, නමුත් වැඩිවෙමින් පවතී
ත්රිමාණ මුද්රණය සඳහා ප්ලාස්ටික්, ලෝහ සහ පිඟන් මැටි ඇතුළු බොහෝ ද්රව්ය තිබේ. කෙසේ වෙතත්, ද්රව්ය විකල්ප ගණන එන්නත් අච්චු ගැසීමේ දී තරම් පුළුල් නොවේ. ත්රිමාණ මුද්රණය හරහා සාදන ලද කොටස්වල යාන්ත්රික ගුණාංග වෙනස් විය හැකි අතර, කොටස් බොහෝ විට එන්නත් අච්චු කරන ලද කොටස් වලට වඩා අඩු ශක්තියක් සහ කල්පැවැත්මක් පෙන්නුම් කරයි, නමුත් නව වර්ධනයන් සමඟ මෙම පරතරය අඩු වෙමින් පවතී.
සුදුසු වන්නේ: ලාභ මූලාකෘති; අභිරුචි සංරචක; ෆොටෝපොලිමර් දුම්මල සහ නිශ්චිත තාප ප්ලාස්ටික් සහ ලෝහ වැනි ද්රව්ය-විශේෂිත දුම්මල.
5. වේගය
ඉන්ජෙක්ෂන් මෝල්ඩින්: මහා පරිමාණ නිෂ්පාදනය සඳහා ඉක්මන්
එය සූදානම් වූ පසු, ඉන්ජෙක්ෂන් මෝල්ඩින් කිරීම සාපේක්ෂව ඉතා වේගවත් වේ. ඇත්ත වශයෙන්ම, චක්රය තත්පර කිහිපයක් සිට මිනිත්තු කිහිපයක් දක්වා ගත විය හැක්කේ කොටස් සිය ගණනක් සහ දහස් ගණනක් ඉක්මනින් නිෂ්පාදනය කිරීමට හැකි වීම සඳහා ය. කෙසේ වෙතත්, ආරම්භක අච්චුව සැකසීමට සහ සැලසුම් කිරීමට වැඩි කාලයක් ගතවේ.
සුදුසුම දෙය: සම්මත මෝස්තර සහිත ඉහළ පරිමාණ නිෂ්පාදනය.
ත්රිමාණ මුද්රණය: බොහෝ මන්දගාමී, විශේෂයෙන් විශාල අයිතම සඳහා
විශේෂයෙන් විශාල හෝ වඩාත් සංකීර්ණ කොටස් සඳහා ඉන්ජෙක්ෂන් මෝල්ඩින් කිරීම ත්රිමාණ මුද්රණයට වඩා සැලකිය යුතු ලෙස වේගවත් වේ. එක් එක් ස්ථරය තනි තනිව මුද්රණය කිරීම, විශාල හෝ වඩාත් සවිස්තරාත්මක කොටස් සඳහා පැය ගණනක් හෝ දින ගණනක් ගත විය හැකිය.
සුදුසු වන්නේ: මූලාකෘති නිර්මාණය, කුඩා කොටස් හෝ ඉහළ පරිමාවකින් යුත් නිෂ්පාදනයක් අවශ්ය නොවන සංකීර්ණ හැඩතල.
6. ගුණාත්මකභාවය සහ නිමාව
ඉන්ජෙක්ෂන් මෝල්ඩින්: හොඳ නිමාවක්, ගුණාත්මකභාවයක්
ඉන්ජෙක්ෂන් මෝල්ඩින් මගින් නිපදවන ලද කොටස් සුමට නිමාවක් සහ විශිෂ්ට මාන නිරවද්යතාවයක් ඇත. ක්රියාවලිය ඉතා පාලනය කර ඇති අතර, එහි ප්රතිඵලයක් ලෙස ස්ථාවර උසස් තත්ත්වයේ කොටස් ලැබේ, නමුත් සමහර නිම කිරීම් සඳහා පසු-සැකසීම හෝ අතිරික්ත ද්රව්ය ඉවත් කිරීම අවශ්ය විය හැකිය.
සුදුසු වන්නේ: තද ඉවසීම් සහ හොඳ මතුපිට නිමාවක් සහිත ක්රියාකාරී කොටස්.
ත්රිමාණ මුද්රණය සමඟ අඩු ගුණාත්මකභාවය සහ නිමාව
ත්රිමාණ මුද්රිත කොටස්වල ගුණාත්මකභාවය බොහෝ දුරට රඳා පවතින්නේ මුද්රණ යන්ත්රය සහ භාවිතා කරන ද්රව්ය මත ය. සියලුම ත්රිමාණ මුද්රිත කොටස් දෘශ්ය ස්ථර රේඛා පෙන්වන අතර සාමාන්යයෙන් පසු-සැකසීම අවශ්ය වේ - වැලි දැමීම සහ සුමට කිරීම - හොඳ මතුපිට නිමාවක් ලබා දීම සඳහා. ත්රිමාණ මුද්රණයේ විභේදනය සහ නිරවද්යතාවය වැඩිදියුණු වෙමින් පවතින නමුත් ක්රියාකාරී, ඉහළ නිරවද්යතාවයකින් යුත් කොටස් සඳහා එන්නත් අච්චු ගැසීමට සමාන නොවිය හැකිය.
සුදුසු වන්නේ: මූලාකෘතිකරණය, පරිපූර්ණ නිමාවක් අවශ්ය නොවන කොටස් සහ තවදුරටත් පිරිපහදු කරනු ලබන මෝස්තර.
7. තිරසාරභාවය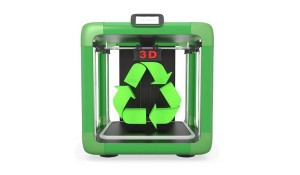
ඉන්ජෙක්ෂන් මෝල්ඩින්: එතරම් තිරසාර නොවේ
ඉන්ජෙක්ෂන් මෝල්ඩින් මඟින් ස්පෘස් සහ ධාවකයන් (භාවිතා නොකළ ප්ලාස්ටික්) ආකාරයෙන් බොහෝ ද්රව්යමය අපද්රව්ය නිපදවයි. එසේම, මෝල්ඩින් යන්ත්ර සැලකිය යුතු ශක්තියක් පරිභෝජනය කරයි. කෙසේ වෙතත්, කාර්යක්ෂම සැලසුම් මගින් එවැනි අපද්රව්ය අවම කළ හැකිය. තවමත්, බොහෝ නිෂ්පාදකයින් දැන් එන්නත් මෝල්ඩින් ක්රියාවලියේදී ප්රතිචක්රීකරණය කරන ලද ද්රව්ය භාවිතා කරයි.
වඩාත් සුදුසු වන්නේ: ඉහළ පරිමාවකින් යුත් ප්ලාස්ටික් නිෂ්පාදනය, නමුත් වඩා හොඳ ද්රව්ය මූලාශ්ර ලබා ගැනීම සහ ප්රතිචක්රීකරණය සමඟ තිරසාර උත්සාහයන් වැඩි දියුණු කළ හැකිය.
ත්රිමාණ මුද්රණය: ඇතැම් අවස්ථාවලදී පාරිසරික වශයෙන් අඩුවෙන් හායනය වීම
මෙයින් අදහස් කරන්නේ ත්රිමාණ මුද්රණය වඩාත් තිරසාර විය හැකි බවයි, මන්ද එය කොටස නිර්මාණය කිරීමට අවශ්ය ද්රව්ය ප්රමාණය පමණක් භාවිතා කරන අතර එමඟින් අපද්රව්ය ඉවත් කරයි. ඇත්ත වශයෙන්ම, සමහර ත්රිමාණ මුද්රණ යන්ත්ර අසාර්ථක මුද්රණ පවා නව ද්රව්ය බවට ප්රතිචක්රීකරණය කරයි. නමුත් සියලුම ත්රිමාණ මුද්රණ ද්රව්ය සමාන නොවේ; සමහර ප්ලාස්ටික් අනෙක් ඒවාට වඩා අඩු තිරසාර වේ.
සුදුසු වන්නේ: අඩු පරිමාවක් සහිත, ඉල්ලුම මත නිෂ්පාදනය අපද්රව්ය අවම කිරීම.
ඔබේ අවශ්යතා සඳහා වඩා හොඳ කුමක්ද?
භාවිතඑන්නත් අච්චු ගැසීමනම්:
- ඔබ ඉහළ පරිමාණයේ නිෂ්පාදන ධාවනයක් පවත්වාගෙන යනවා.
- ඔබට අවශ්ය වන්නේ ශක්තිමත්ම, කල් පවතින, හොඳම ගුණාත්මකභාවය සහ කොටස්වල අනුකූලතාවයි.
- මූලික ආයෝජනය සඳහා ඔබට ප්රාග්ධනය ඇති අතර ඒකක විශාල සංඛ්යාවක් සඳහා අච්චු පිරිවැය ක්රමක්ෂය කළ හැකිය.
- සැලසුම ස්ථාවර වන අතර එතරම් වෙනස් නොවේ.
භාවිතත්රිමාණ මුද්රණයනම්:
- ඔබට මූලාකෘති, අඩු පරිමාවක් සහිත කොටස් හෝ ඉතා අභිරුචිකරණය කළ නිර්මාණ අවශ්ය වේ.
- ඔබට නිර්මාණයේ නම්යශීලීභාවය සහ වේගවත් පුනරාවර්තනය අවශ්ය වේ.
- එක් වරක් හෝ විශේෂිත කොටස් නිෂ්පාදනය කිරීම සඳහා ඔබට ලාභදායී විසඳුමක් අවශ්ය වේ.
- ද්රව්යවල තිරසාරභාවය සහ ඉතිරිකිරීම් ප්රධාන ගැටළුවකි.
නිගමනයක් ලෙස, ත්රිමාණ මුද්රණය සහ ඉන්ජෙක්ෂන් මෝල්ඩින් යන දෙකටම ඒවායේ ශක්තීන් ඇත. ඉන්ජෙක්ෂන් මෝල්ඩින් ඉහළ ප්රමාණයකින් නිෂ්පාදනය කිරීමේ වාසිය ගැන පුරසාරම් දොඩන අතර, ත්රිමාණ මුද්රණය නම්යශීලී, මූලාකෘතිකරණය සහ අඩු පරිමාවක් හෝ ඉහළ අභිරුචිකරණය කළ නිෂ්පාදනයක් ලෙස කියනු ලැබේ. එය ඔබේ ව්යාපෘතියේ හරියටම කොටස් මොනවාද යන්න දක්වා අඩු වේ - නිෂ්පාදනය, අයවැය, කාලරේඛාව සහ නිර්මාණයේ සංකීර්ණත්වය අනුව වෙනස් අවශ්යතා.
පළ කිරීමේ කාලය: පෙබරවාරි-07-2025